STEP 5: BUILDING THE TOP SECTION
The nose cone is the most complex part, therefore I decided to print it. Also the cone to connect from the 60 mm tube to 80 mm is a 3D printed part.
Nose and Tube Cones
I use Fusion360 to design my parts for 3D printing, Cura for slicing and a Creality Ender 5 printer. Below you can find the STL files for the nose cone and the tubes connector.
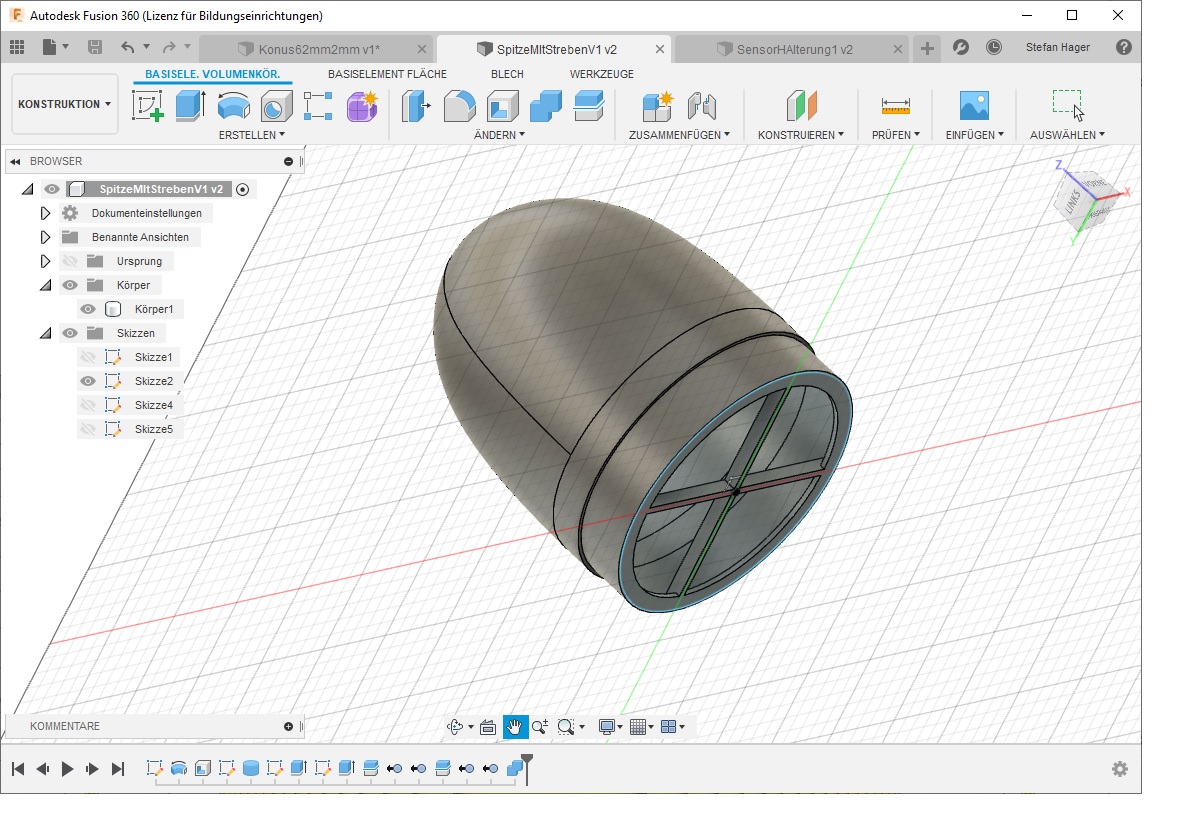
The nose cone gets printed:
3D Printing Files
Cone62To82mm.stl:
NoseCone.stl:
Core Stage Top Section
Inside the fairing section is my electronics bay. It contains a KeyCam (which sits in a 3D printed holder) and a simple altimeter.The nose cone can be removed and is just connected with a rubber band.
The Falcon Not So Heavy
The right booster has a mass of 237 g without engines, the left booster 238 g. The weight of the complete core stage is 365 g with parachute but even without engines. 1100 grams launch mass for the entire rocket is well within my limits and fits pretty good with the initial Open Rocket calculations.
Mass in Grams: Right booster incl. parachute : 237 Left booster incl. parachute : 238 Core lower section : 220 Top section incl. parachute : 106 Nose cone (core stage) : 45 KeyCam : 14 Engines (8xC and 4xB) : 240 : ====================================== Total mass : 1100